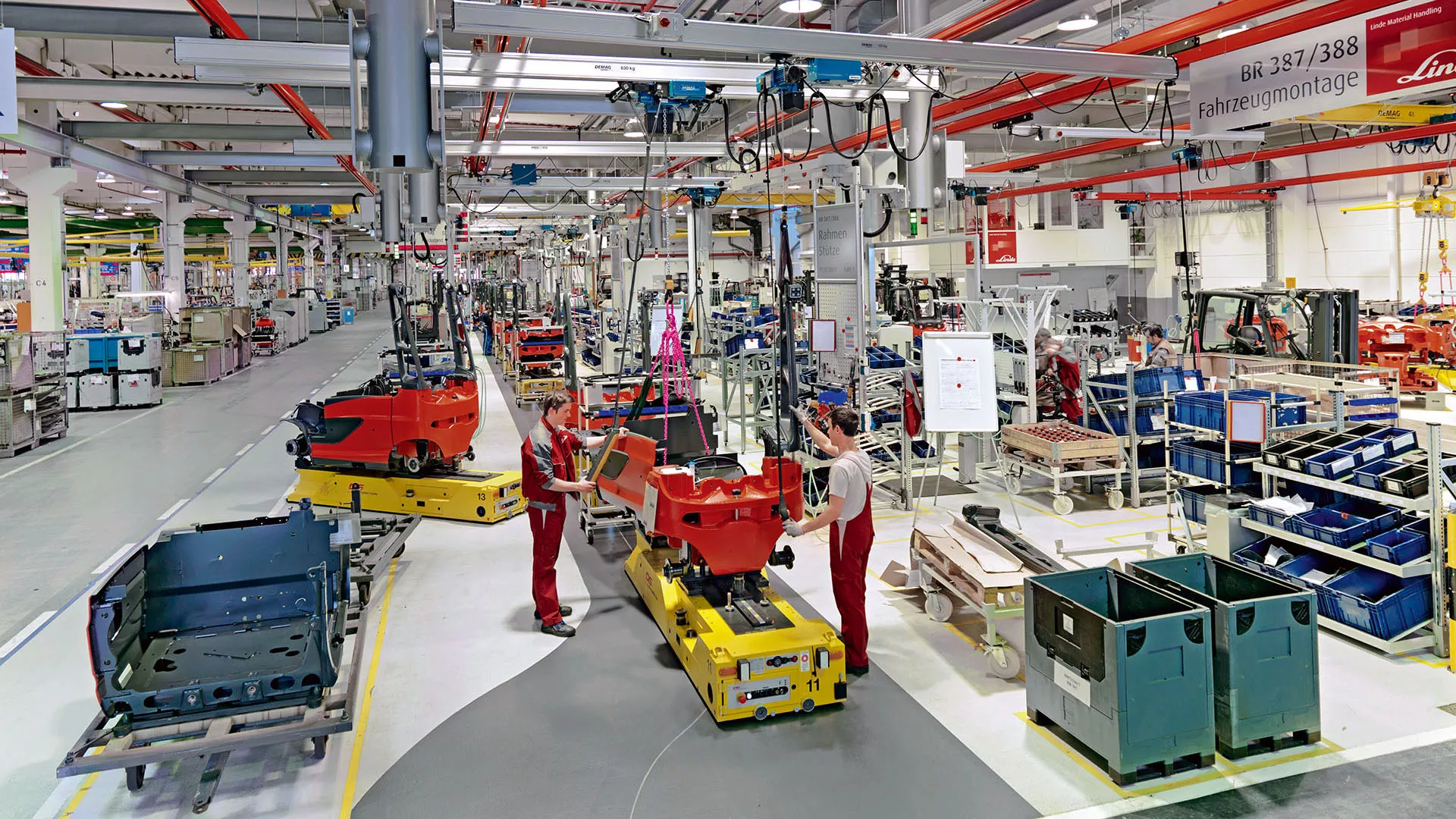
Versatile manufacturing structures
Linde Material Handling
Perfect combination
Light crane system with strong benefits
The E range of forklift trucks built by Linde Material Handling features efficiency and high performance. Linde already attaches great importance on performance and flexibility in production – and opted for the proven Demag KBK light crane system in the assembly line for its new BR 387 and 388 forklift truck ranges.
One system to meet all needs
Crane bridges optimised to reduce their weight, compact dimensions and versatile mounting connections – the KBK light crane system offers a wide variety of benefits. Linde decided in favour of combinations made of KBK aluminium and steel profile sections and an intelligent connection between the crane systems and the process control system. This arrangement enables monitoring functions to be integrated and adapted to match changed cycle conditions.
Prepared for the future
When the assembly workers have learned how to work according to the production cycles, Linde plans to switch over to continuous production. The cranes supplied by Demag are already prepared for this step: friction-wheel travel drives can be disengaged and the crane can slowly move along the line by means of the positive connection.
- Combination of aluminium and steel profile sections
- Ergonomic solutions for indexed assembly operations
- Connection to the main control system
Pre-assembly
Pre-assembly with 2 crane levels
The forklift production line starts in the pre-assembly zone, where the workers use a 4-tonne EPDE suspension crane to lift counterweights, turn them on a turning device and then place them on an AGV that is waiting to receive them. A locking mechanism limits the turning angle of the hook, thus ensuring a reliable and continuous supply of power to the attached turning device. All functions are controlled by means of a Demag DST control pendant. Thanks to the crane runway, which is suspended from the roof superstructure, the floor remains free of any additional runway supports. This arrangement ensures that there is sufficient space for the assembly operations and the flexibility required in the processes.
Also suspended from the roof superstructure are the KBK suspension crane installations, which are mounted immediately below the suspension cranes. Operating on this pair of tracks are two KBK single-girder suspension cranes that are equipped with Demag DC-Pro chain hoists. These units are used by the assembly workers to install other components, such as steering shafts, on-board chargers and voltage transformers. One of these push-travel cranes is also fitted with a control panel for powered screwdrivers. For ergonomic reasons, it is mounted on a smooth-running KBK trolley.
Thanks to the use of KBK II-R profile sections, featuring integrated conductor lines, as crane girders, the chain hoists and the operating panel are supplied with power without the need for any additional cables. The current collectors connected to the KBK II system load trolleys tap power direct from the conductor lines.
Forklift production to meet specific needs
For the assembly of its range of forklift trucks, Linde Material Handling utilises the benefits of the KBK light crane system. The factory planners decided in favour of a combination of weight-optimised suspension cranes made of aluminium profile sections and crane runways made of KBK steel profile sections.
Staggered crane runways for optimised crane bridge lengths
Installed above the 3.5 metre-wide assembly line and the lateral staging zones are two crane runways, which are arranged eight metres apart. The Linde planning team considered that this length would impose ergonomic limitations due to the size of the push-travel single-girder suspension cranes that operate in this area. For this reason, the decision was made to install two further crane runway rails between these profile sections. This staggered arrangement enabled crane bridges with a maximum length of six metres to be installed, which alternatively cover the staging zones on the right or left as well as the central assembly line. Another crane, which is used to support a stamping device that applies the chassis numbers, utilises the two inner tracks that span a distance of four metres.
Monitoring the assembly cycles
Ten suspension cranes operate above the assembly line. Four of them are of double-girder design and are fitted with electric friction-wheel travel drives for smooth and easy travel. The workers use them to pick up the modules to be installed which are staged at the side of the assembly line and which weigh more than 15 kilograms. In accordance with a defined cycle time, the AGVs more forward again another five metres to the next station in the cycle. Before this movement cycle can begin, all travelling hoists must be moved away from the centre of the assembly line to the end of the relevant crane bridge. This line-clearing operation is monitored by travel-motion limit switches, which are installed on every crane bridge. The signals are transferred to the central control system by means of the Demag DCL conductor line. The central control system indicates the current operating cycle status via traffic lights at each workplace. Only when all travelling hoists have been moved out of the line and, therefore, all lamps are green, can a new cycle begin.
KBK profile section combinations
In order to improve the assembly workers' daily working conditions even further, the factory planning engineers at Linde Material Handling decided in favour of crane bridges that have a low deadweight – made up of the Aluline 180 aluminium profile section. In this way, they utilise one of the strengths of the tried and tested KBK light crane system: the aluminium profile sections can be combined with crane runways that are made of steel profile sections.
Parallel to the assembly line, further workplaces were established for pre-assembly work. Here, overhead guards and pressure tanks are prepared for assembly on the line, for example. In this area, too, the workers benefit from lighter crane bridges made of aluminium for the push-travel cranes, which also travel smoothly on crane runways that are constructed of steel profile sections.
Power supply via integrated conductor lines
KBK II-R profile sections, which are fitted with integrated conductors, are used at Linde Material Handling both for the crane runways as well as for the assembly and pre-assembly lines. This arrangement enables the crane bridges to be supplied with power without the need for any trailing cables, thus achieving a high level of flexibility. A total of eight parallel crane runways cover the entire production area and are suspended at the same height, also in order to meet changing requirements.
Universal cranes with compact dimensions
The two final assembly cycles involve the installation of the lifting masts and the batteries. Cranes that have higher load capacities and special design features were needed for this work inside the assembly line. On the one hand, the mast has to be tilted when it is installed, which results in inclined pull. In addition, although they are performed in the immediate vicinity of each other, the various steps have to be completed separately.
The solution: two single-girder overhead travelling cranes that have a span of 14.15 metres travel on one runway. To enable them to approach each other as closely as possible, the end carriages were designed to form an asymmetric arrangement. Any possible collisions are prevented by a two-stage safety cut-off system. The type EPDE crane that is used for installation of the lifting masts is equipped with a 3.2-tonne DR-Pro rope hoist, which has a double rope guide that permits inclined pull of the load. To ensure that the horizontal forces are safely handled when the mast is tilted, the two end carriages were also equipped with a total of four travel drives, which hold the crane in position down to the last millimetre. The second crane, a type EPKE, had to achieve particularly low approach dimensions. For this reason, a 2.5-tonne DC-Pro chain hoist was installed. Thanks to the use of frequency inverters for three directions of motion, the loads can be precisely and easily positioned.
Cable-connected control pendants
For control of the cranes, Linde decided to use only cable-connected DST control pendants for fatigue-free operation. For the large number of assembly steps that have to be carried out in the available space, the planning engineers prefer to keep the workers in direct contact with the various processes at the forklift truck production facility.
Slewing cranes with optimum freedom of movement
The planning engineers at Linde integrated a further component from the KBK light crane system in their forklift truck production line. Besides a pillar-mounted slewing jib crane, they installed six wall-mounted slewing jibs, which take up no floor space. For this solution, mounting plates were prepared with standard bore hole templates and attached to the supporting superstructure of the building. Installed on these mounting plates are wall-mounted slewing jibs, which are made up of KBK profile sections that offer a particularly low deadweight. Adjustable limitation of the slewing motion ensures that they can be used without any risk of collision with other equipment. If required, the cranes can be detached from their mounting plates and re-located within the bay for maximum flexibility.