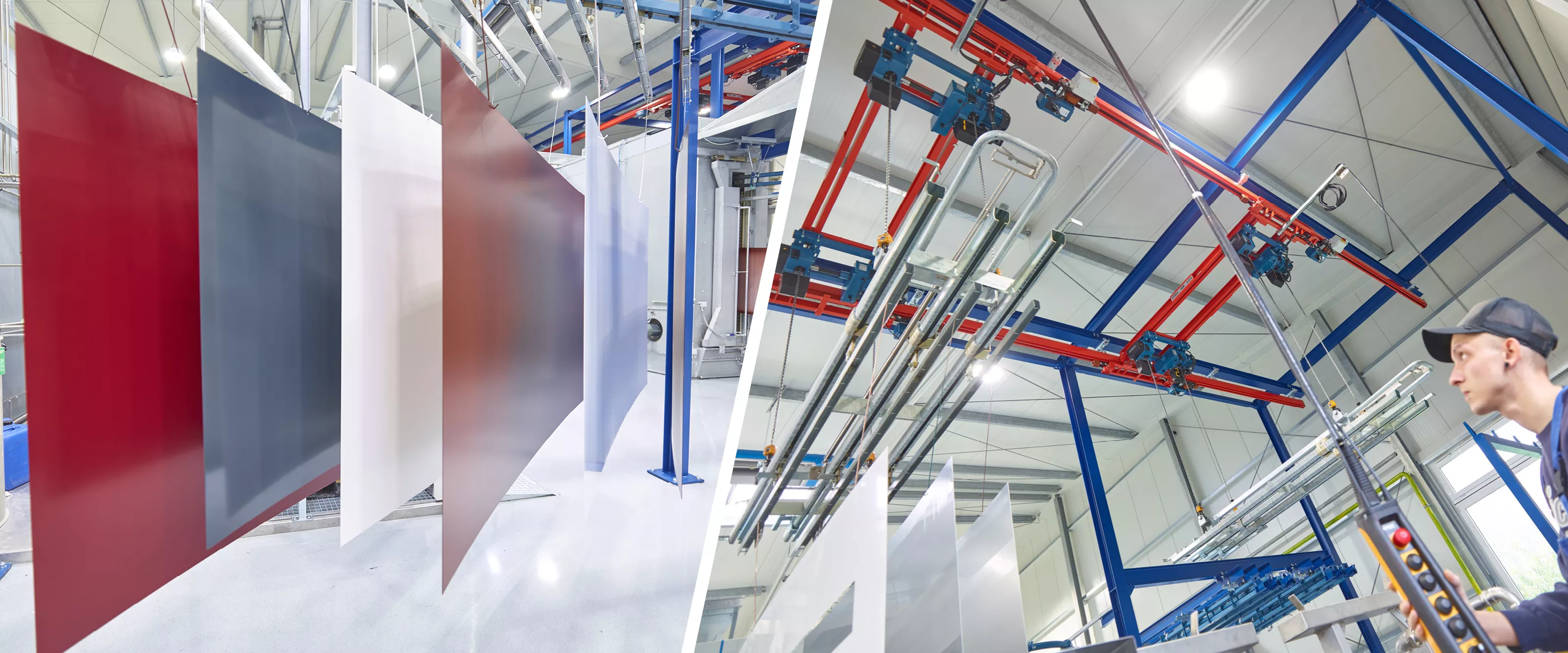
Collegamento flessibile dei diversi processi di produzione con il sistema di gru modulare KBK
Demag Sistema di carroponte modulare KBK
Preparare manualmente - produrre automaticamente
Per la costruzione del suo nuovo impianto di rivestimento di componenti in alluminio, un produttore di elementi per porte ha scelto deliberatamente di combinare una linea di trasporto automatica e un processo di preparazione manuale. Il nesso fra questi processi è rappresentato da un carroponte sospeso dotato di paranchi a catena doppi con comando in parallelo.
Mecklenburger Bauelemente GmbH è una società controllata al 100% da Rodenberg Türsysteme AG, specialista e leader di mercato nel settore dei pannelli per porte su misura.
L'impianto gestito dalla filiale di Cramonshagen vicino a Schwerin è il più settentrionale delle quattro sedi di produzione tedesche dell'azienda. Nel complesso inaugurato nel 1992, si producono su ordinazione elementi per i pannelli delle porte e per i telai, prodotti semilavorati e pannelli in alluminio.
Dato l'incremento delle richieste, l'impianto di verniciatura a disposizione era già sfruttato al massimo, in uso 24 ore su 24 per 6 giorni su 7. Al fine di alleggerire il lavoro di questo impianto e di creare capacità supplementari, il gestore ha pensato alla costruzione di un secondo reparto di verniciatura. In soli nove mesi, è stato costruito qui un nuovo edificio, dove è stato messo in funzione il complesso impianto.
All'interno del capannone, che misura ben 1.600 m², si svolgono tutte le fasi di lavorazione legate alla verniciatura, dalla preparazione al rivestimento delle superfici. Sono presenti quattro cabine di spruzzatura per l'applicazione delle vernici a polvere, collegati ai forni di cottura mediante un convogliatore power-and-free automatico progettato e installato dalla ditta Sapp di Eslohe. Il reparto di produzione è preceduto da un'area dedicata alle operazioni preliminari, con dieci bagni d'immersione. Qui, in particolare, il gestore si concentra sui processi manuali destinati a introdurre le successive operazioni automatizzate.
Michael Kock, Direttore del dipartimento di Produzione presso Mecklenburger Bauelemente GmbH, spiega i motivi di questa decisione: “Presso il nostro stabilimento, si progettano e si producono tutti i componenti in base alle specifiche del cliente: dalla piccola applicazione di dieci centimetri quadrati fino a piastre grandi anche quattro metri e mezzo. Il materiale deve essere lavorato nella sequenza in cui arriva, non deve essere necessario suddividerlo prima in funzione delle dimensioni.”
Con un impianto completamente automatico, bisognerebbe ogni volta impostare prima i tempi d'immersione dei componenti e il processo in fase preliminare sarebbe ogni volta diverso. “Ecco perché abbiamo optato per una zona manuale a monte e per un sistema di carroponte controllabile manualmente che trasferisca i pezzi nei bagni. Quest'idea si è poi rafforzata in considerazione delle esperienze fatte con il nostro impianto già esistente, affidabilmente in uso da ben 17 anni.”
L'integrazione nel processo
Il processo di produzione a Cramonshagen è progettato per un'elevata flessibilità. I pezzi vengono consegnati direttamente all'area di verniciatura in base agli ordini dalle vicine aree di produzione, poi vengono identificati con il codice a barre e quindi si agganciano manualmente a uno dei 60 carrelli dell'impianto power-and-free.
Kock dice: “Gli elementi in arrivo, a prescindere dalle dimensioni, vengono trasferiti direttamente ai fini del processo di produzione in corso per il rivestimento superficiale in funzione delle richieste, vengono quindi lavorati rapidamente, per poi essere riportati in produzione, dove si svolge l'assemblaggio finale.”
Per la movimentazione dei componenti, è stata installata una birotaia del sistema di carroponte modulare KBK Demag, con carrelli di sollevamento di Demag Cranes & Components. Grazie alla struttura modulare del sistema KBK, è stato possibile adattare perfettamente l'impianto alle esigenze del caso. Il fissaggio alla struttura del capannone è sato realizzato utilizzando le sospensioni KBK, che fanno parte del sistema. Una via di corsa lunga 35 m, costituita da sezioni profilate KBK-II-R, si estende sull'area di raccolta, sui bagni e sulla stazione di trasferimento verso le altre attrezzature per la movimentazione dei materiali. L'uso di sezioni profilate con linee conduttrici integrate mantiene le linee di alimentazione protette all'interno delle sezioni del profilo, il che elimina la necessità di cavi lungo il binario.
Su questa birotaia, si muovono due carrelli dello stesso tipo, ottimizzati in termini di altezza e dotati ognuno di due doppi paranchi a catena LDC-Pro-D. Portata per gancio: 125 kg. Ogni paranco a catena doppio dispone di svolgimenti di catena sincronizzati meccanicamente, che consentono una movimentazione precisa delle traverse. Con questa soluzione costruttiva, le catene durano più a lungo, perché non sono necessari rinvii supplementari. I paranchi a catena a due fasi hanno due velocità di sollevamento, ovvero 4 e 16 m/min, perciò permettono un posizionamento preciso, senza rinunciare allo spostamento rapido delle traverse.
Posizionamento di precisione
Considerando l'intensità dell'utilizzo durante il turno di lavoro, i paranchi a catena sono dimensionati in maniera tale da rientrare nel gruppo FEM 4m. Per una protezione durevole, i mezzi di sollevamento sono verniciati a polvere, ottenendo così una protezione anticorrosione di qualità anche nella versione standard. Il posizionamento esatto dei carrelli sulla via di corsa si ottiene grazie ai gruppi motore di traslazione a ruota d'attrito di tipo RF 125, con il motore E22-C del sistema modulare, che può funzionare a 7 o 27 m/min, a seconda delle esigenze. Come funziona: un operatore sposta il primo carrello con la traversa agganciata a quattro ganci (figura a pagina 5), portandolo precisamente nella posizione finale della tratta di convogliamento, concludendo così il percorso. A questo punto, si possono disporre sulla traversa tre carrelli carichi di elementi di alluminio, uno accanto all'altro.
Infine, l'operatore può sollevare la traversa dalla via di corsa, spostare il carrello al di sopra di uno dei quattro bagni di sgrassaggio, per poi abbassare il carico dentro i bagni stessi. Una volta iniziato il processo di immersione, il carrello è già pronto per il processo di movimentazione successivo, ovvero per uno dei dieci bagni singoli dove i prodotti da verniciare vengono sottoposti al decapaggio e al risciacquo e vengono così preparati all'applicazione della vernice. Trascorso il tempo all'interno delle vasche, prestabilito singolarmente, la traversa viene risollevata dal bagno. Mediante un apposito selettore, si possono spostare separatamente i paranchi con due svolgimenti di catena e la traversa viene posta in posizione obliqua,
“Questo processo è importantissimo ai fini di una movimentazione rapida”, afferma Kock. “Infatti, posizionando i paranchi in obliquo, acceleriamo il deflusso del liquido prima del passaggio al bagno successivo.”
I due paranchi a catena doppi si controllano mediante una pulsantiera DST 7 cablata, disposta su un braccio di supporto che ne permette l'utilizzo in posizione ergonomica dalla passerella lungo i bagni. Grazie all'apposito selettore, si possono impostare le funzioni di utilizzo singolo o in tandem (figura a pagina 4). La funzione tandem garantisce il posizionamento preciso dei quattro svolgimenti di catena quando i paranchi sono utilizzati insieme.
In caso di arresto imprevisto del paranco a catena, per esempio se dovesse attivarsi un finecorsa, si ferma immediatamente anche il secondo paranco. Concluso l'ultimo bagno, il terzo carrello preleva la traversa (figura a pagina 7) e la depone sul percorso di convogliamento, analogamente alla stazione di prelievo. Da qui, i componenti raggiungono il convogliatore automatico, per ricevere finalmente il rivestimento cromatico richiesto dal cliente (figura a pagina 2).
“A seguito dell'avvio del nostro impianto, avevamo pensato a una capacità compresa fra 40 e 60 carrelli all'ora, a seconda delle singole grandezze costruttive”, afferma Kock. “Combinando processi automatici e movimentazione manuale, siamo stati in grado di raggiungere l'obiettivo in tempi brevissimi. L'impianto del carroponte per la movimentazione dei componenti contribuisce largamente alla nostra capacità di raggiungere gli obiettivi prefissati in termini di flessibilità e qualità.”
Galleria fotografica
Galleria fotografica
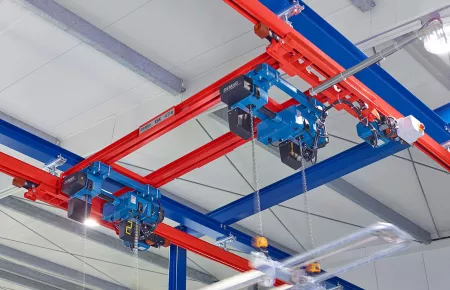
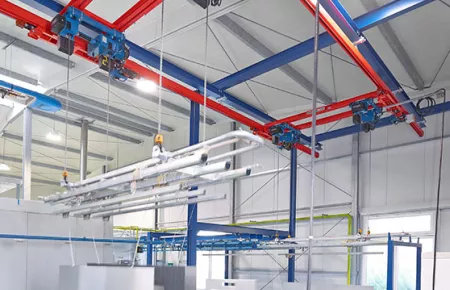
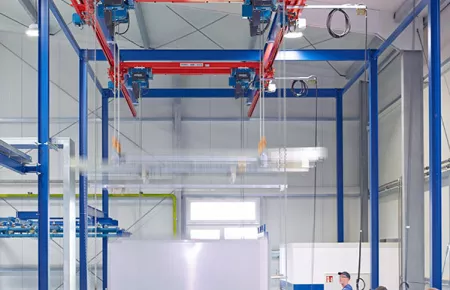
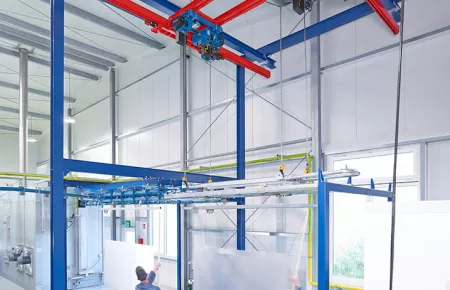