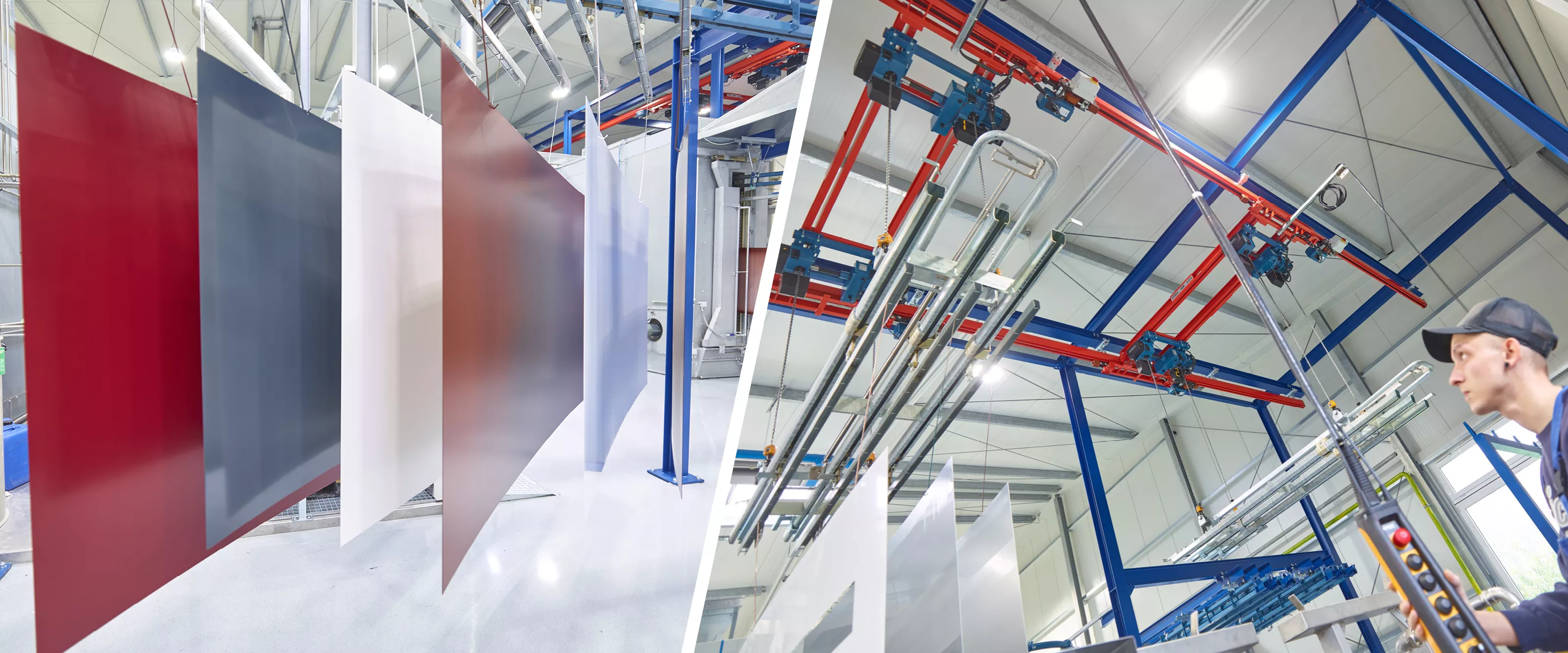
L’ensemble modulaire KBK permet l’enchaînement en toute flexibilité de différents processus de fabrication
Demag Ensemble modulaire KBK
Préparation manuelle – production automatisée
Lors de la construction d’une nouvelle installation de revêtement pour des pièces en aluminium, un fabricant d’éléments de porte a délibérément opté pour un système associant une ligne de transport automatique et un prétraitement manuel. Un pont suspendu équipé de palans à double sortie de chaîne pouvant être commandés en parallèle, assure la liaison entre ces processus.
L’entreprise Mecklenburger Bauelemente GmbH est une filiale à part entière de la société Rodenberg Türsysteme AG qui compte parmi les spécialistes leaders du marché des panneaux de porte d’entrée fabriqués sur mesure. L’usine de la filiale de Cramonshagen, près de Schwerin, est le site de production situé le plus au nord des quatre sites allemands. Inauguré en 1992, ce complexe fabrique sur commande des éléments pour panneaux de porte tels que cadres, produits semi-finis et panneaux en aluminium.
Par suite de la hausse des carnets de commande, l’installation de revêtement existante fonctionnait depuis quelque temps à plein régime, 24 heures sur 24 et 6 jours sur 7. Afin de délester cette installation et de créer des capacités supplémentaires, l’exploitant a décidé de construire un deuxième hall dédié au processus de revêtement. En l’espace de neuf mois seulement, un nouveau bâtiment a été construit sur le site et cette installation complexe a été mise en service.
Toutes les étapes du processus de revêtement, de la préparation à la finition de surface, se déroulent dans ce hall qui couvre 1600 m². Quatre cabines de pulvérisation servant à l’application de la peinture en poudre et les fours de cuisson sont reliés par une installation de convoyage power-and-free à fonctionnement automatique, conçue et installée par la société Sapp Anlagenbau, basée à Eslohe. L’aire de fabrication est précédée d’une zone de préparation des commandes équipée de dix bains d’immersion. L’exploitant utilise ici délibérément des processus manuels pour amorcer les processus automatisés qui suivent.
Michael Kock, directeur de production chez Mecklenburger Bauelemente GmbH, explique les raisons de cette décision : « Sur notre site, tous les composants sont planifiés et fabriqués selon les spécifications du client, de la petite application de dix centimètres carrés aux panneaux d’un mètre et demi sur trois. Nous voulons accrocher le matériel au fur et à mesure de son arrivée et non pas avoir à le trier d’abord en fonction de ses dimensions ».
Sur une installation automatisée, il faut à chaque fois régler à l’avance les temps d’immersion des composants et le processus de prétraitement est à chaque fois différent. « Par conséquent, nous avons opté pour une zone de préparation manuelle et des ponts à commande manuelle pour alimenter les bains. Nous avons été confortés dans notre choix par l’expérience réalisée avec notre installation existante qui assure un service fiable depuis 17 ans. »
Intégration dans les processus
Le processus de fabrication à Cramonshagen repose sur une flexibilité maximale. En fonction des commandes, les pièces sont livrées directement depuis les halls de fabrication voisins dans le hall de chargement, enregistrées à l’aide de code-barres et accrochées manuellement dans l’un des 60 chariots de l’installation de convoyage power and free.
Kock: « Quelle que soit leur taille, les éléments qui arrivent sont directement intégrés, en fonction de la commande traitée, dans le processus de traitement de surface, immédiatement traités puis renvoyés ensuite en production pour le montage final. »
La manutention des composants est assurée par une voie birail de l’ensemble modulaire KBK Demag équipée de chariots de levage de Demag Cranes & Components. La conception modulaire du système KBK a permis d’adapter avec précision l’installation aux exigences. La fixation a été réalisée avec des suspensions KBK propres au système sur la structure du bâtiment. Une voie de pont d’une longueur de 35 m constituée de profilés KBK-II-R, avec une largeur de voie de 3 mètres, enjambe la zone de réception, les bains et la station de transfert vers les autres équipements de manutention. L’équipement des profilés de voie avec une ligne de contact intégrée protège l’alimentation en énergie à l’intérieur du profilé, rendant ainsi un câblage le long de la voie superflu.
Trois chariots de construction identique, dont la hauteur de construction a été optimisée, se déplacent sur cette voie birail. Ils sont équipés chacun de deux palans à double sortie de chaîne de type LDC-Pro-D. La capacité de charge par crochet est de 125 kg. Chaque palan à double sortie de chaîne dispose de sorties de chaîne à synchronisation mécanique, qui permettent la manutention précise de traverses. Cette construction assure une durée de vie plus longue des chaînes, étant donné qu’aucun renvoi de chaîne supplémentaire n’est nécessaire. Les palans à chaîne qui fonctionnent avec deux vitesses de levage de 4 et 16 m/min, permettent un positionnement précis ainsi qu’une manutention rapide des traverses.
Positionnement précis
Les palans à chaîne sont conçus selon le groupe FEM 4m en raison des contraintes élevées auxquelles ils sont soumis au cours d’un même poste de travail. Afin d'assurer une protection durable des appareils de levage, ceux-ci bénéficient de série d’une protection de haute qualité contre la corrosion, obtenue grâce à un revêtement par poudre. Le positionnement exact des chariots sur la voie est assuré par des mécanismes de translation à roue de friction de type RF 125 équipés d’un moteur E22-C du système modulaire ; ceux-ci se déplacent au choix à une vitesse de 7 ou 27 m/min. Le déroulement est le suivant : un opérateur déplace le premier chariot-palan avec la traverse accrochée à quatre crochets (photo page 5) jusqu’à la position finale de la ligne de transport et achève ainsi le parcours de transport. Trois chariots transportant des éléments en aluminium peuvent à présent être transférés côte à côte et prise en charge par la traverse.
Ensuite, l’ouvrier soulève la traverse de la voie, déplace le chariot au-dessus de l’un des quatre bains de dégraissage et y fait descendre la charge. Lorsque l’immersion dans le bain commence, le chariot est prêt pour la prochaine étape de manipulation pour l’un des dix bains différents, dans lesquels les produits en aluminium à revêtir sont décapés, rincés et préparés pour l’application suivante de la peinture. Lorsque la période prescrite pour chaque élément dans le bassin d’immersion est écoulée, la traverse est soulevée hors du bain. Un sélecteur permet de déplacer individuellement les palans à deux sorties de chaîne et de placer la traverse en position inclinée.
« Cette opération est essentielle pour garantir la rapidité de la manutention », explique Kock. « En effet, en inclinant les palans, nous accélérons l’écoulement du liquide avant le passage au bain suivant. »
La commande des deux palans à double sortie de chaîne s’effectue à l’aide d’une boîte à boutons DST 7 commandée via une flèche dans une position ergonomique depuis la passerelle qui longe les bains. Un sélecteur permet de régler les fonctions utilisées en service individuel ou en mode tandem (photo page 4). Lors de l’utilisation commune des palans, le mode tandem assure le positionnement précis des quatre sorties de chaîne.
En cas d’arrêt involontaire d’un palan à chaîne – par exemple, suite à l’activation d’un interrupteur de fin de course – le deuxième palan est lui aussi immédiatement immobilisé. Une fois le dernier bain achevé, le troisième chariot prend en charge la traverse (photo page 7) et l’intègre – de façon similaire au poste de réception – dans la ligne de transport. Depuis cet endroit, les pièces passent dans le flux automatique de la ligne de transport et reçoivent enfin la couche de peinture souhaitée par le client (photo page 2).
« Après la phase de démarrage de notre installation, nous avions prévu un rendement de 40 à 60 chariots par heure – en fonction des différentes tailles », explique Kock. « Nous avons atteint cet objectif en peu de temps en combinant des processus automatiques avec des manipulations manuelles. L’installation affectée à la manipulation des composants apporte une contribution décisive à la réalisation des objectifs que nous nous sommes fixés en termes de flexibilité et de qualité. »
Galerie d'images
Galerie d'images
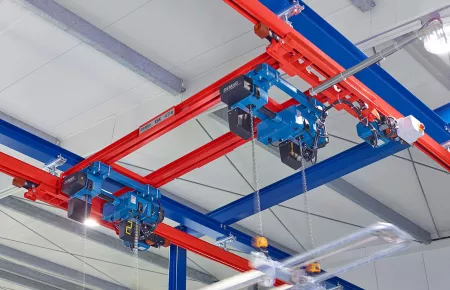
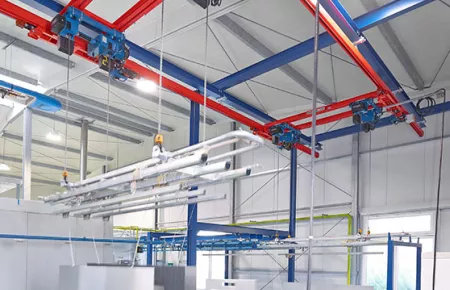
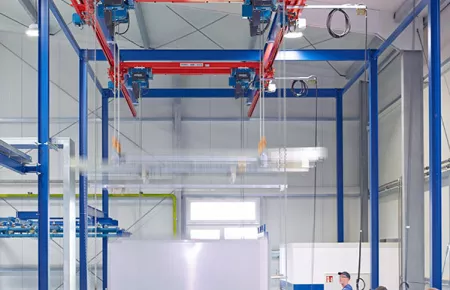
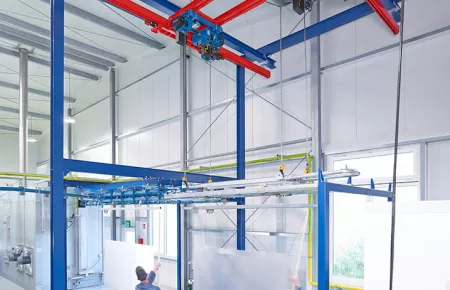