Demag Dedrive Pro frequency inverters 880: Specially designed for crane applications
- Demag CraneControl: application program for crane drives
- Direct Torque Control
- Integrated electronic load-sway reduction
- Many safety functions included
From the crane manufacturer – for crane manufacturers. Terex Material Handling presents a new range of Demag inverters. This new range of Dedrive Pro 880 inverters has been specifically developed for applications in crane technology. One of the central features of these new inverters is Direct Torque Control (DTC). This feature makes it possible to directly control the speed and torque without having to track speed and position for travel applications through sensors and encoders. As a result, the inverters offer highly dynamic vector control of long-travel, cross-travel and hoist drives, thus reducing the amount of sensitive sensor technology required on the crane itself.
The inverters are equipped with Demag CraneControl, a complete application program for crane drives. This means that you have ‘on board’ precisely the functions that a crane manufacturer requires. These functions include brake control with brake feedback evaluation, torque memory and a system check. It is also possible to select field weakening operation with partial load and synchronous control for operating several hoist units.
Saved as complete software solutions in the application program of the Dedrive Pro 880 inverters, these functions considerably reduce the costs and work involved in engineering for the crane manufacturer. The crane operator can thus make use many practical and innovative control functions.
The model-based load-sway reduction is a crane-specific function of the Dedrive Pro 880 inverter that is as important as it is innovative. This model-based function without sensors effectively reduces the load sway based on a mathematical model. In practice, this function paves the way for both considerably higher handling rates and even safer crane operation.
Of course, the application program also includes the crane-specific service functions, such as elapsed operating time counter for the crane, load spectrum for the hoist unit and starting frequency for the brake. Remote diagnosis allows you to view the crane control system from anywhere and makes it possible to output fault and error messages. Thanks to this preventive maintenance principle, this means higher crane availability for you.
The new Dedrive Pro 880 frequency inverters are available as a complete series in the Demag drive systems product range for crane drives with 0.55 kW to 560 kW power ratings. Nine wall-mounted units with varying frame sizes (R1 to R9) and two free-standing models (R10 and R11) complete the range.
Convenient operation is not only guaranteed during the configuration phase, but also in daily operation: a removable control panel with intuitive menu serves as a man/machine interface. Thanks to their design, including varnished PCBs, and because of their overload capability, the inverters are ideally suited to crane operation, often in rough conditions, with many starting-and-stopping-operations. Despite these conditions, they achieve a long service life and comply with all – including industry-specific – system requirements.
Further information
Many safety functions
In addition to the standard Safe Torque Off (STO) function, the optional safety function module of the Dedrive Pro 880 inverter supports further standard-compliant functions such as Safe Stop (SS1), Safe Brake Control (SBC), Safe Limited Speed (SLS) and Safe Maximum Speed (SMS). Owing to the built-in safe-control system, crane designer engineers do not need to add this system as a extra component, thus reducing complexity, simplifying the control architecture and cutting costs.
Synchronous control and master/follower operation
Several Dedrive Pro 880 inverters in master/slave mode can implement synchronous control of up to four hoist units, enabling precise handling, even of highly sensitive loads. This function is also programmed into the application program of the inverter as is the master/follower operation with torque tracker in Drive-to-Drive (D2D) mode. No additional hardware is needed. The torque tracker ensures that torque is shared between two mechanically connected geared motors.
A ‘communicative’ drive
Thanks to many interfaces, the Dedrive Pro 880 is network-enabled and extremely ‘communicative’. It features digital and analogue I/O extensions and interfaces for signal evaluation of different pulse generators. It can also be equipped with communication modules for various standards such as PROFIBUS DP, Ethernet/IP, Modbus TCP, PROFINET IO and – for use of the safety function module – PROFIsafe.
Remote diagnosis
Another inverter module is fitted with an integrated web server for remote access to the inverter data. The user can access the website of this module via a 3G modem or with standard PC, tablet and smartphone. The module can also record process and drive data, which are saved internally or transferred to a database. The remote diagnosis module also issues warning and fault messages, thus allowing for timely preventive maintenance measures to ensure higher crane availability.
Fast commissioning
Thanks to the many crane-specific configuration options in the application program, crane design engineers can dispense largely with costly programming and still implement sophisti-cated functions tailored exactly to the requirements of materials handling and crane operation.
Your Contact
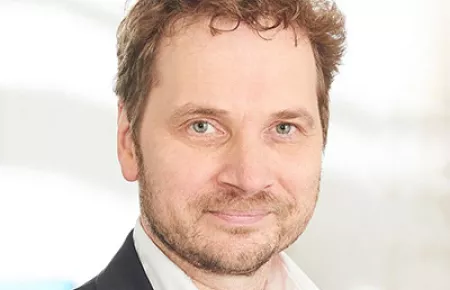
Christoph Kreutzenbeck
Ruhrstrasse 28
58300 Wetter
Germany