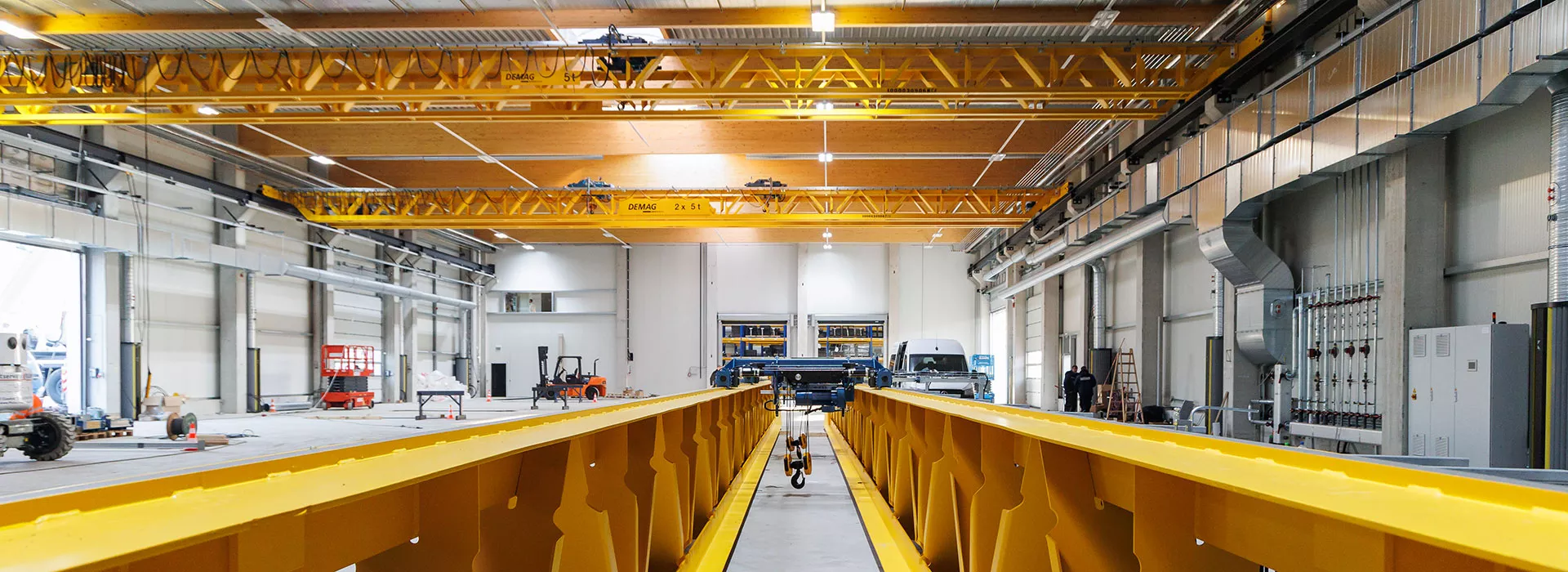
Material flow safely timed
Krampe Fahrzeugbau GmbH speeds up production with V-type cranes from Demag
Quality on wheels from Münsterland
Krampe Fahrzeugbau supplies tailor-made vehicles for agriculture and has been manufacturing with a high level of vertical integration in Münsterland for over a century. Long-standing certified Demag partner Aloys Strotdresch e. K. used Demag’s wide range of components for an equally tailored material handling concept using Demag crane and lifting technology.
Company
Vehicles from Münsterland, Germany are well-established and popular in the agriculture sector. Krampe Fahrzeugbau GmbH has been manufacturing tractor-drawn body, two-way and earth moving tippers as well as halfpipe and hook lift semi-trailers as tippers in Coesfeld since 1918 and distributes them worldwide to almost 40 countries. The company has been manufacturing at its Coesfeld site for over four decades and relies on a high level of vertical integration. Customers experience “quality on wheels” as their individual wishes are met. With this strategy, the company is now in its fourth generation of continuous growth.
Requirement
Besides trailers, two workshops have also been built on the Krampe company premises in recent months. Managing Director Robin Krampe: "We need space – for building the bodies as a core component of the body tippers and for our customer service. By creating these new buildings, we want to achieve our ambitious goal of increasing our production capacity by 25%."
Large and weighty components are welded and assembled in the new 3,600 m2 workshop for body construction. This task is divided between a welding robot and individual workstations for manual special construction. In order to achieve a rapid throughput of up to 8 vehicles per working day in the future, ergonomic considerations are key when setting up the workstations. Better lighting conditions in production also play a role, as does the air conditioning of the workstations and an ergonomic control concept for the support required for lifting and transport operations.
Krampe has implemented XXL size flow production for this purpose. Those responsible were faced with the challenge of achieving a smooth flow of materials from station to station. Certified Demag partner Aloys Strotdresch, along with Demag, supported them in the planning of a new material flow concept and assembled several cranes in the new workshops.
Aloys Strotdresch e.K. in brief
Strotdresch is a family business founded in 1938 and now successfully run by the third generation. The company is a certified partner and an authorised Demag workshop. The two companies have enjoyed a trusting relationship for more than 60 years. Strotdresch sends its crane technicians directly to the customer for on-site repairs and general overhauls and also offers the necessary acceptance tests by experts. Customers can also purchase Demag components or complete solutions from Strotdresch.
Solution
Six double-girder V-type cranes with a span of 29.44 metres and a load capacity of 5 tonnes each travel on a common 90-metre-long crane runway. Up to six welded assemblies or bodies can be transported simultaneously overhead from one work step to the next – and if required, one or two work stations can also be connected to each other.
Strotdresch recommended the Demag V-type as a crane girder, as the bionic profile design enables a high load capacity with a low dead weight (around 17%) and improved vibration behaviour (around 30%) compared to conventional box-section girders. A second reason is that those responsible at Krampe have endeavoured to give their employees a well-lit working environment, so that as much daylight as possible falls on the workplaces thanks to the 90-metre-long roof glazing. With six double-girder cranes, the shape of the profile makes a decisive difference – the V-type with its tapered diaphragm joints allows plenty of light to pass through and thus contributes to a safe and agreeable lighting atmosphere in the new production workshops. As soon as the daylight is no longer sufficient, modern LED lighting provides good and efficient illumination inside the workshop.
A Demag single-girder V-type crane with a load capacity of 5 tonnes and a span of 20.44 metres was installed in the second, 800 m² workshop, which is reserved for customer service. Among other things, it facilitates the handling of heavy components at the three service assembly stations.
All the cranes are equipped with Demag DRC-10 radio control systems. Up to three transmitters can be logged on per crane. For employees, this means that they can easily change cranes at the push of a button. The operation of individual cranes can thus be easily transferred from employee to employee. Transmitters can be swapped in seconds and are also protected against unwanted activation. The very safe, robust and interference-resistant radio transmission method used by Demag radio control systems ensures smooth crane operation throughout the new assembly and service workstations.
Special features
All six cranes can be conveniently operated by radio in all axes (long and cross travel, hoist unit) using a Demag DRC-10 single-hand transmitter. The display on the controller shows the respective load capacity and operating status of the crane.
The optical anti-collision devices ensure safe crane operation and provide a useful convenience and assistance function for the operator. The crane electric equipment continuously monitors and intervenes automatically as soon as a programmed distance is exceeded. The crane stops or slows down depending on the customer’s requirements. In the event of a changing operating situation, the distance can of course be reprogrammed.
In cooperation with the Demag project engineers, Strotdresch took over the planning of the entire crane system and was also responsible for the installation of crane runways and cranes – a challenging task because in some cases they worked with an external mobile crane, which moved the 30-metre-long crane girders through the long open rooflight. However, Strotdresch’s experienced team were also able to carry out this crane assembly job efficiently and safely.
Your contact
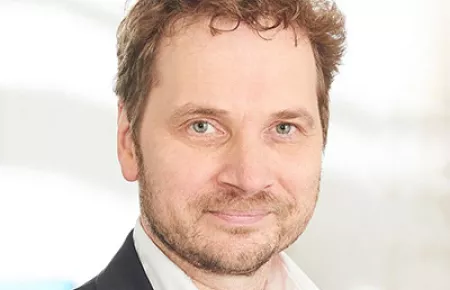
Christoph Kreutzenbeck
Ruhrstrasse 28
58300 Wetter
Germany
Image gallery
Image gallery
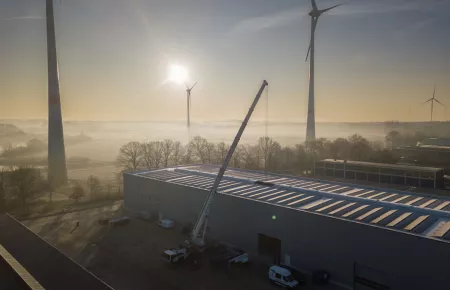
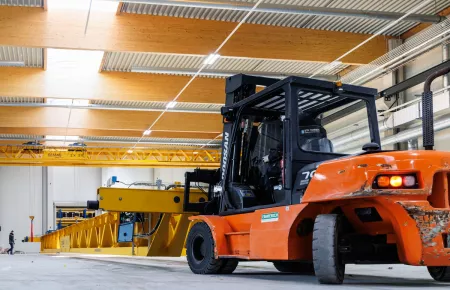
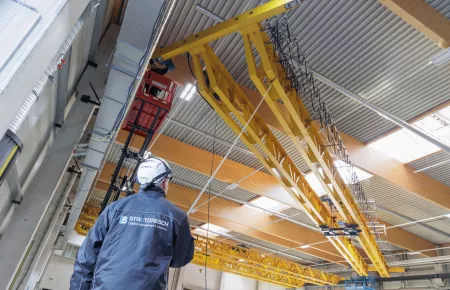
