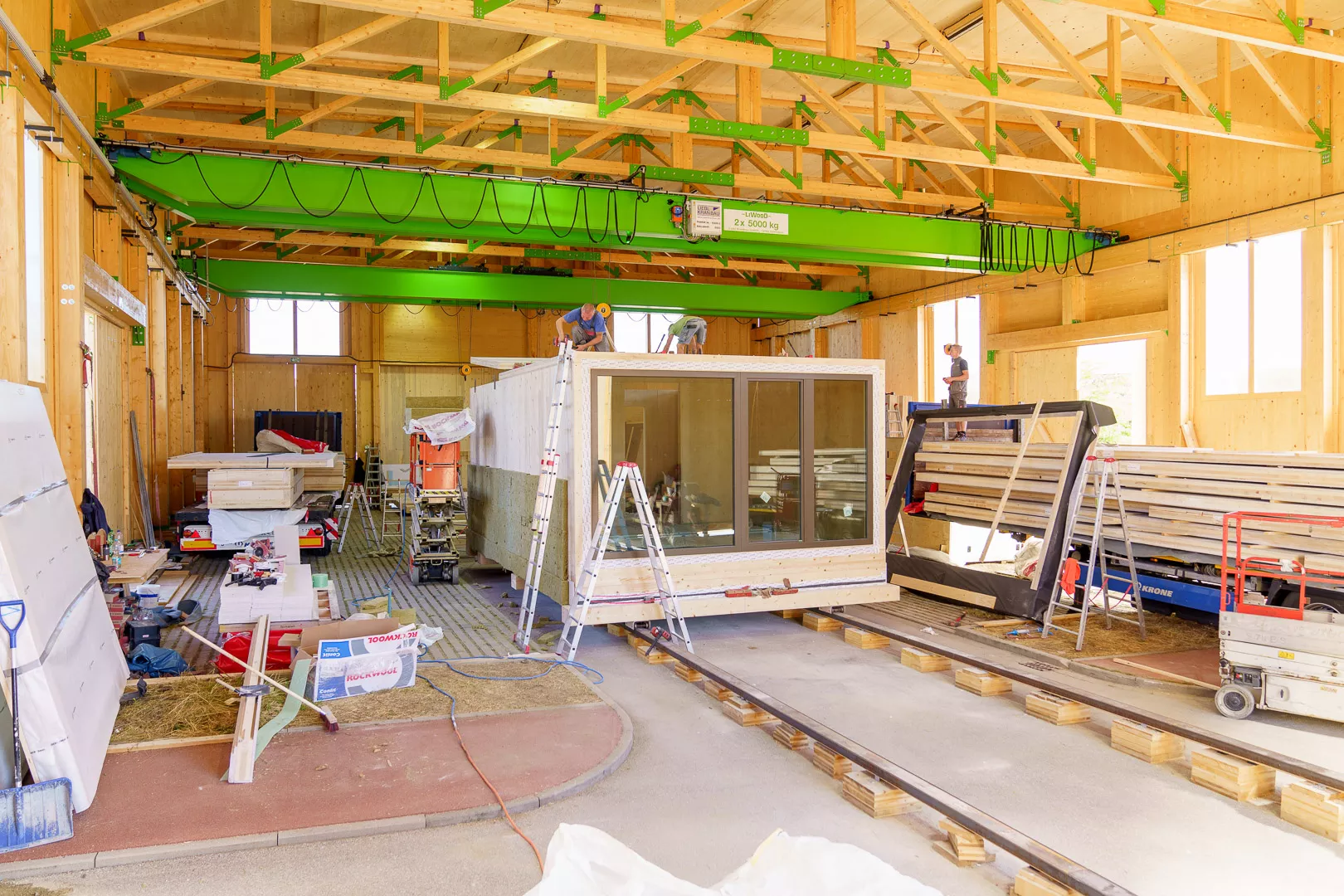
Modular housing construction made of wood
LiWooD produces residential buildings in flow production
Modular housing construction made of wood
Demag components for handling sustainable building materials
LiWooD AG uses a sustainable manufacturing concept for the construction of residential units. The house components are manufactured in a wooden production line directly on the construction site. The key: The production hall moves from construction site to construction site. Demag’s long-standing partner Liebl Kranbau from Ostfildern built cranes, including Demag components and Demag rope hoists, to handle some of the large building elements. Since then, the crane construction partner has supported LiWooD in dismantling and assembling the cranes from site to site.
Company
When LiWooD AG from Munich starts a construction project – usually a multi-storey residential building – it adopts a different approach from what has been customary in high-rise construction for decades. A hall made entirely of wood is first built from prefabricated elements in the immediate vicinity of the construction site. This hall houses the production line, which receives individual parts according to a schedule and builds them into wooden units and entire rooms on site. Indoor cranes provide support during assembly. The industrial and modular design ensures rapid construction progress and increases the quality of both the process and the resulting structures.
LiWooD is very successful with this unique concept. The building material is sustainable, the energy balance is very favourable and the costs are also appealing. The concept, which is still unusual in this country, is also perfectly suited for consolidating residential areas. The estates can be expanded on a modular basis at any time. LiWooD thus creates sustainable settlements and buildings and reduces its CO2 footprint through an efficient production concept.
Requirement
LiWooD employees assemble the modules into complete residential units in a flow production facility. The field factory creates up to 120 m² of living space per day. A module is transported from one assembly station to the next on rails. The individual components such as the bathroom, exterior and interior walls, windows and doors are removed from truck trailers positioned at the sides, placed on the floor module and fastened. Two overhead cranes on a shared crane runway take care of transport to the production line.
The cranes need to enable precise and safe handling of large-volume components and must therefore be robust and designed for a long service life. The sustainability aspect is reflected in the crane system. After each completed project, the assembly hall is dismantled and rebuilt at a new construction site.
The solution experts from Swabia
Liebl Kranbau has an excellent reputation in the industry and stands for decades of experience and innovative system solutions. And, of course, for Swabian entrepreneurial spirit and unbridled ingenuity. Since the company was founded in 1997, it has been on a steady expansion course under the management of its founder Franz Liebl. In Ostfildern near Stuttgart, the family-owned company develops innovative and customer-oriented system solutions that the crane manufacturer installs and maintains at the customer’s premises after completion.
Solution
LiWooD approached the certified Demag partner Liebl Kranbau in Ostfildern, near Stuttgart with this requirement profile. Liebl designed and built two double-girder overhead cranes with a span of 19.44 metres, which travel on a shared 47-metre long crane runway. Demag DRS-M 160 wheel blocks, which have been tried and tested for decades, are also used as trolleys for a wide range of crane types. The wheel blocks are combined with Demag offset geared brake motors and Demag ZBF90 drives to form an extremely compact and powerful drive unit.
Both the travel speed of the two cranes and the lifting speed of the four Demag rope hoists, each with a load capacity of 5 tonnes and a hook path of 6 metres, are infinitely adjustable to enable precise positioning of the large-format timber modules. This means that the hoist can be lifted and lowered in a range of 0.7 to 4 m/min – whereby the speed is less relevant than the precise positioning capability.
As a rule, the rope hoists hold the components in position until LiWooD employees in the hall have completely connected them to the adjacent components. The holding brakes and prevention of the load from dropping are therefore just as important as the travel drives. Another safety feature is the overload protection that the hoists are equipped with.
Demag components were an obvious choice for Liebl Kranbau here. Not only because the company is a long-standing certified Demag partner and maintains a good partnership with the manufacturer, but also because the components used guarantee a very high level of safety and a long service life. Sustainability also plays a key role in the selection of components.
Special features
On the one hand, the location where the cranes are used is unusual. Frequent erection of the temporary production hall, including the crane runway and overhead travelling crane, as well as the corresponding dismantling are uncommon and place stress on the components. The cranes – in particular their connecting elements – have been designed and reinforced from the ground up for these operating conditions.
The crane experts at Liebl Kranbau, who are very familiar with this recurring task, are responsible for the correct assembly and disassembly of the crane. This service was already agreed during the project planning phase of the cranes – as an integral part of the “all-round no-worries” package offered by the Certified Demag Partner for this exceptional crane system.
Another special feature is not so surprising when you consider the construction of both the production hall and the houses built by LiWooD: The runway rails are mounted on wooden beams over their entire length. This concept is also proving to be a success.
Image Gallery
Image Gallery
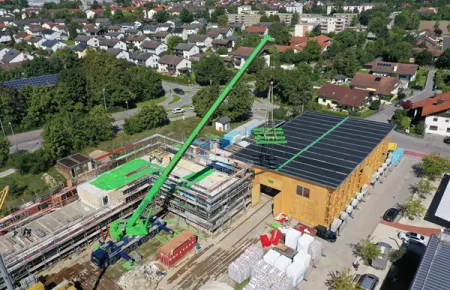
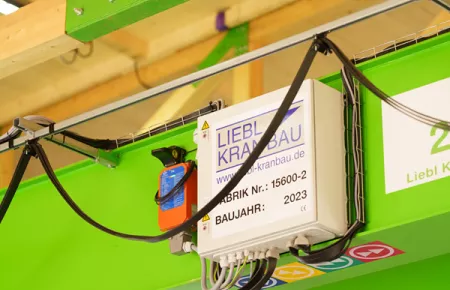
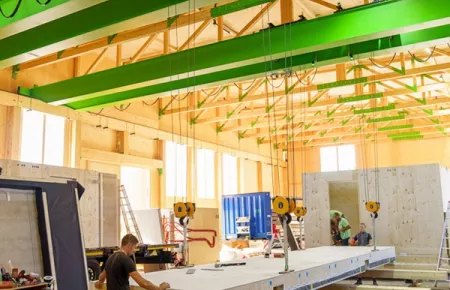
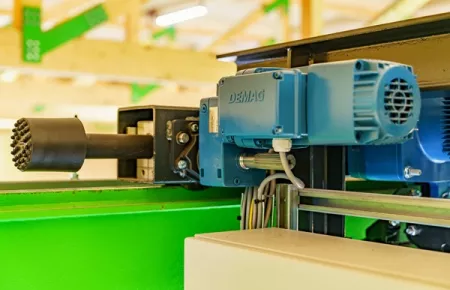