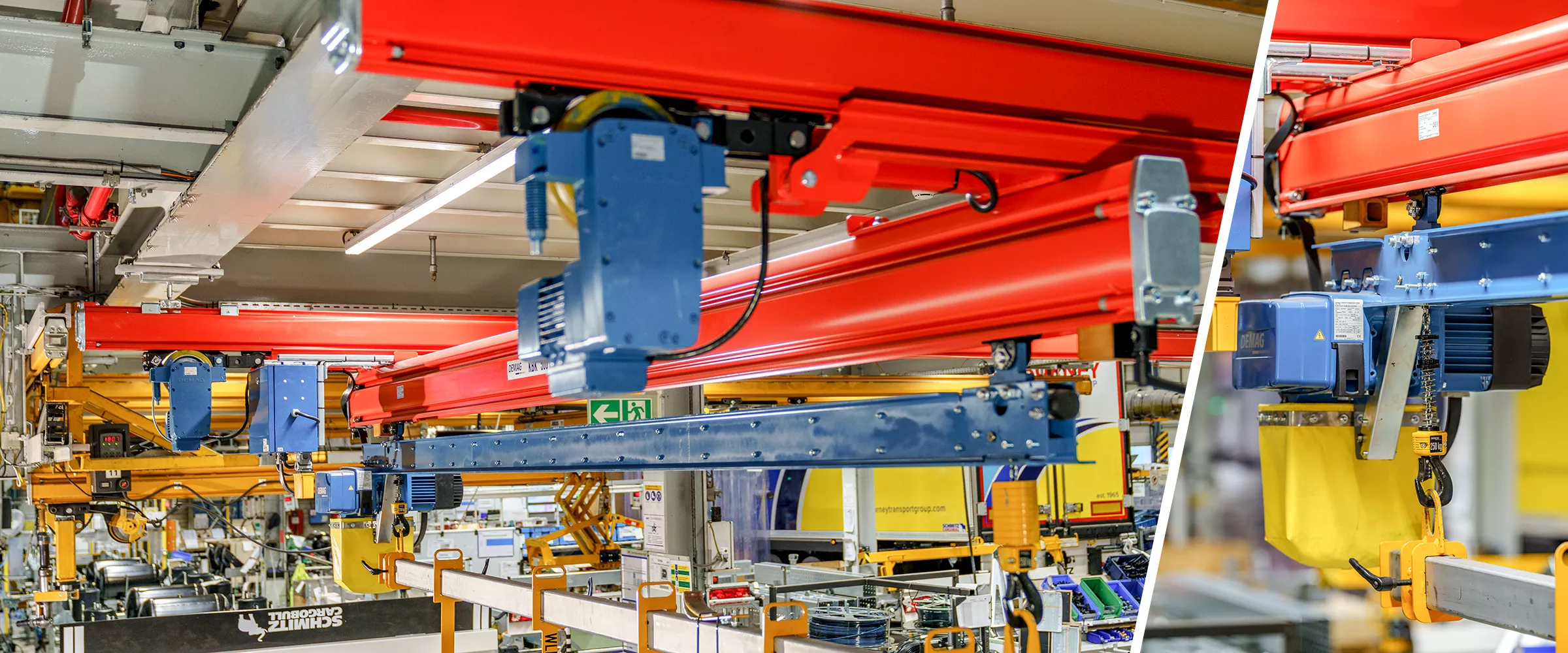
KBK system with low-headroom trolley used in assembly of truck trailers
Schmitz Cargobull opts for ergonomic handling
Perfect interaction for handling complex components
Customer
Schmitz Cargobull AG is one of the most well known manufacturers of high-quality truck trailers for transporting all kinds of cargo on the roads of Europe. Its product range is correspondingly wide to meet many needs. Besides classic box trucks and tippers, the company also manufactures curtainsiders, container chassis, swap bodies and chassis as well as transport refrigeration units.
At its production facility in Vreden, Münsterland, the vehicle manufacturer still builds its products in the same region where Franz Heinrich Schmitz established the family-run company as a forge in 1892. Since its establishment, Schmitz Cargobull has been shaped by successful innovations and promotes convenience as well as performance and safety in long-distance transport by building and continuously improving truck trailers. Schmitz Cargobull produces around 42,500 units every business year.
Requirement
Chassis for box-body vehicles are manufactured in a continuous assembly operation on one of the production lines at the plant in Vreden. One step in production is assembly of the brake loom, which runs from the brake unit to the brakes on the axles and can be up to four metres in length. The loom is a complex item. It consists of several pieces of equipment that are only connected by various media lines and signal cables.
The task is to transport the brake loom from pre-assembly to the location where it is installed in the assembly line. Due to the size of the loom, it is better to transport it overhead. However, because of its length and the difficulty of handling the load with conventional hoists, it poses a challenge in practice. The handling solution needs to be integrated into the customer’s radio control concept that is used throughout the company.
Solution
The Demag engineers developed a solution for Schmitz Cargobull based on the modular KBK light crane system, which has been used for many assembly tasks for decades.
Following pre-assembly, the brake looms are suspended from a 4 metre-long spreader. The spreader is raised by a Demag KLDC double chain hoist and transported some seven metres by the KBK system to the neighbouring production line. Here, the workers install the loom in the chassis (which is located upside down on the transport system).
The KBK system has electric travel in all directions. Two travel (20 and 5 m/min) and lifting speeds (12 and 3 m/min) ensure that the spreader and brake loom can be moved quickly and precisely positioned. The DRF 200 drives are from our own production and were specially developed for the KBK system.
The extended load attachment points of the KLDC double chain hoist are ideal for the use case at Schmitz Cargobull. The attachment points can be varied from 400 mm to 4,600 mm. The KLDC ensures that the lifting motion is mechanically synchronised, which means that the entire brake loom can be uniformly positioned over all pick-up points. At the same time, the low-headroom design of the hoist trolley with a short C dimension permits optimum utilisation of the available headroom (which is quite small in this case).
A safety feature: An operating limit switch on all DC chain hoists ensures that the chain hoist is safely switched off when it reaches its highest and lowest limit positions. This doubles the safeguard for the crane operator to avoid any load sway. The options that Demag recommended for this application, and Schmitz Cargobull selected, include buffers that can be easily installed and repositioned. They make it easy to adjust the handling system to match any changes in the brake loom.
“A tailor-made, efficient and ergonomic solution”
Interview with Demag Sales Engineer Thorsten Koslowski-Zobel, who managed the project engineering for the KBK installation at Schmitz Cargobull:
Which challenges were there for technical implementation of the handling system for the trailer production?
There were a few – for example the building structure and the wish to control the installation via an existing radio system. The complexity of this project is reflected by the intensive interaction with the decision-makers at Schmitz Cargobull. Together, we sought the best possible solution and, for that reason, we also revised some aspects of the quotation several times until it was the optimum fit.
Which special technical features of the Demag components are there in this project?
The special features include the KLDC double chain hoist with its trolley and optimised hook dimension. The double chain lead-off with a 4000 mm fixed hook centre distance ensures that the hooks are always mechanically synchronized. For the KBK equipment, it is worth mentioning that it travels under electric power in all directions and that it is controlled by the radio system provided by Schmitz Cargobull.
What were the reasons for this combination of KBK light crane system and DC double chain hoist in this project?
For handling long or awkward, but also light products, this combination is simply ideal. And using our comprehensive construction kit system, a tailor-made, efficient and ergonomic solution can always be found for handling and assembly needs.
Re “tailor-made”: If Schmitz Cargobull wants to manufacture other or additional trailer types on this line – can the KBK system then still be used?
That is no problem at all. The system is completely flexible. As long as the overall length of the brake loom does not change significantly, only small adjustments are necessary. That is why the KBK system is so popular in the automotive industry, for example. It can continue to be used every time a model changes and is, therefore, a long-term investment.
Image gallery
Image gallery
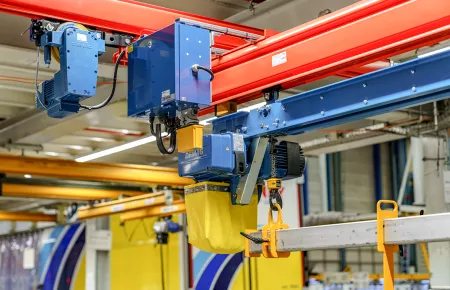
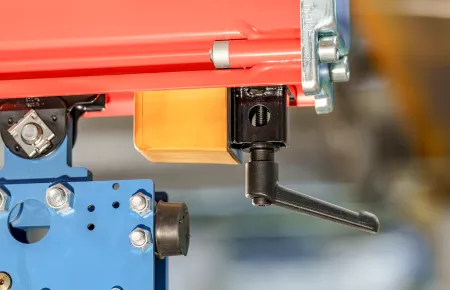
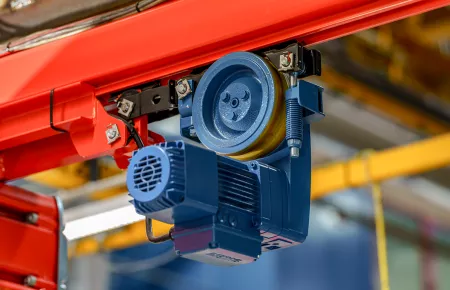
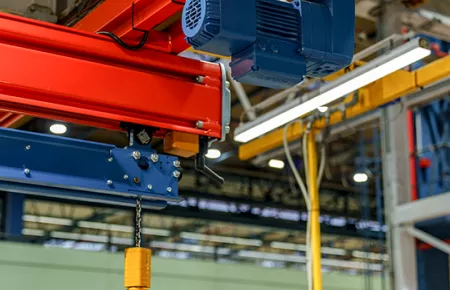