Higher handling rates thanks to double lifting solution
- Fully automated Demag roll-shipping store for Laakirchen Papier AG
- Two process cranes each fitted with two open winch crabs that can travel independently of each other
- Increased performance thanks to new travel and control concept
Demag has installed a fully automated paper roll store with two Demag process cranes for the Austrian company Laakirchen Papier AG. The cranes work in the roll shipping store at the modernised paper factory located in Laakirchen, Upper Austria. Thanks to the installation of two open winch crabs that can travel independently on each Demag crane, the owner benefits from additional flexibility and higher load handling rates.
As part of the Heinzel Group, Laakirchen Papier AG produces paper for publications and packaging on its two PM10 and PM11 paper machines at the location in Laakirchen. Following the conversion and modernisation work, paper machine PM10 specialises in the production of lightweight corrugated base paper made from waste paper for environmentally friendly packaging solutions. This provides a not inconsiderable increase in its production capacity. At the same time, production capacity for SC paper used for magazines, catalogues and printed advertising material has been extended to paper machine PM11. The resulting investment in a new paper-roll shipping store is an important part of the growth strategy pursued by Heinzel Group, which has set itself the goal of becoming the most competitive and eco-friendly paper factory in Europe.
The automated Demag shipping store with the two process cranes accommodates the entire output of the PM10 paper machine. The two Demag cranes, which are each equipped with two crabs that can travel independently of each other, also provide for high load handling rates during peak periods.
“With our new fully automated crane store we can load approx. five trucks per hour. We save around 30% loading time compared to a ground storage system”, explains Dr Thomas Welt, CEO of Laakirchen Papier AG. The open winch units are fitted with vacuum lifting devices, which can be used to store and retrieve the unpacked rolls of paper quickly and, above all, gently. Each crane is designed in such a way that it can store or retrieve single or pairs of rolls measuring up to 1,500 mm in diameter, 3,300 mm in width and weighing up to 4.5 t. This innovative technology enables the system to perform up to 104 roll movements per hour.
“Due to the limited store dimension requirements and simultaneous just-in-time deliveries to our customers, the four independently travelling crabs at Laakirchen Paper AG ensure that the system is sufficiently flexible also during peak periods. Particularly in view of the available space, this represents a performance parameter for this customised crane solution”, explains Gerhard Lange, Demag PRC Paper Senior Project Manager.
Additional information
With its industrial locations at Zellstoff Pöls AG (Austria), Laakirchen Papier AG (Austria), Raubling Papier GmbH (Germany) and AS Estonian Cell (Estonia), Heinzel Group is one of the largest producers of market pulp and magazine paper in Central and Eastern Europe. The product range in Laakirchen forms an ideal supplement to the grades of paper produced by Raubling Papier GmbH in Germany, which was integrated into Heinzel Group in early 2016 and focusses on special corrugated paper. The corrugated base paper made at the Laakirchen and Raubling sites is marketed under the name “starboard”.
To be able to store this production output carefully and to ship it on time, the Laakirchen Papier AG paper factory has invested in a new paper-roll shipping store, which is equipped with two Demag process cranes (33 m span).
Besides the restricted area for storage of the rolls of paper, the loading times, which are limited to five working days, also pose a challenge for this project. Particularly at the beginning of the week, when the roll store is filled to a high level, the trucks that collect the product need to be served very quickly. “To clear the peaks in the paper store, we initially placed emphasis on reducing the number of crane travel operations. This was implemented by installing two crabs on each crane”, explains Markus Otto, Demag Process Cranes sales director. “We have also achieved high performance values since we were able to transfer the fast travel and lifting speeds of our process cranes to this double-crab solution.”
The cranes are precisely positioned at the points specified by the warehouse management system by means of laser position measuring systems. The vacuum lifting device needs less than a second to connect to the rolls of paper by suction. Lifting and lowering speeds of up to 78 m/min are achieved with a load and 120 m/min without a load. The cranes stack the rolls of paper in piles measuring up to 15.05 m in height in an area measuring 2,700 m².
The warehouse management system facilitates high system performance in the store with high handling rates. This is also achieved by high operating speeds and flexible assignment of the travel areas for the two cranes. The automated crane installations satisfy the safety requirements of EC Machinery Directive 2006/42EC, i.e. all safety-related functions are of 2-channel design.
Maximum performance and availability 24/7
The rolls, which are configured to meet individual customer specifications, measure up to 3,300 mm in width and can weigh up to 4,500 kg. The store can accommodate some 8,870 tons of paper when filled to a capacity of 80 per cent. The store is filled around the clock in 24/7 operation. However, goods are only delivered during a period of 69.5 hours per week. In the remaining time, the process cranes, which are controlled by the Demag warehouse management system, optimise the store and prepare any scheduled retrieval operations.
The two process cranes utilise benefits both for handling rolls as well as for power consumption: electric power generated during the lowering and braking operations is fed back into the power supply by smart power recovery units. In this way, the company’s energy footprint is further improved.
Your contact
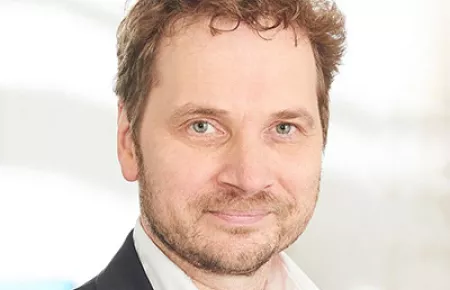
Christoph Kreutzenbeck
Ruhrstrasse 28
58300 Wetter
Germany